Carbon neutral and biodegradable are familiar buzzwords in today’s environmental industry – but has their wide usage blurred their definitions? CEO Darrel Fry of Advanced BioCarbon 3D (ABC3D) is breaking down their precise meanings and providing a prognosis for a bright future where wood replaces all 700 manufactured plastics. But Darrel isn’t an environmentalist; he’s an entrepreneur who cares about simplifying manufacturing in a way that agrees with Mother Earth – all while localizing the workforce and creating opportunity in the growing clean-tech industry.
Darrel’s academic background may be in finance, but his experiences have been focused in the technical and environmental industries. After originally wanting to create a biofuels company, he realized that the process could be used in a more efficient way. He was further inspired by his time as President of Passive Remediation Systems Ltd., a company renowned for using trees to remediate toxins from landfill sites.
When Darrel started working on ABC3D’s concept back in 2008, the appetite for his product wasn’t as fervent; social awareness just wasn’t driving change like it is today. Since incorporating ABC3D in 2016, he’s leading a company that’s determined to be part of the solution, and firmly believes the sense of hopelessness the plastics crisis has created is repairable. He’s spent the last decade innovating and developing a new materials industry that acts in harmony with the planet. In his leisure time Darrel can be found at Red Mountain coaching alpine skiing for Special Olympics athletes or spending time with his family, who have lived in Rossland for six generations.
Tell me about Advanced BioCarbon 3D (ABC3D).
Our mission is to utilize the earth’s resources in a way that acts in harmony with our planet, and to make people’s lives better. ABC3D does that both by producing sustainable advanced materials that enhance quality of life and by providing rewarding green jobs. We’re making non-toxic plastics from wood, a renewable resource, to replace all types of plastics. They’re very compostable, which means they degrade quickly into natural compounds that go back into the earth, just like a plant. Our plastics are carbon negative; they’re engineered grade quality, high-performance, incredibly strong, and heat and chemical resistant. We also produce thermoplastics, thermoset plastics, and carbon fibers – functional and structural – that are electrically conductive. Those are turned into semiconductors and insulators, materials used in batteries, solar cells, sensors, and structural components. Everything we use is recycled and reused and almost any product you can think of can be manufactured from our materials, which creates the opportunity for localized manufacturing and eliminates the challenges that come with shipping products all over the world.
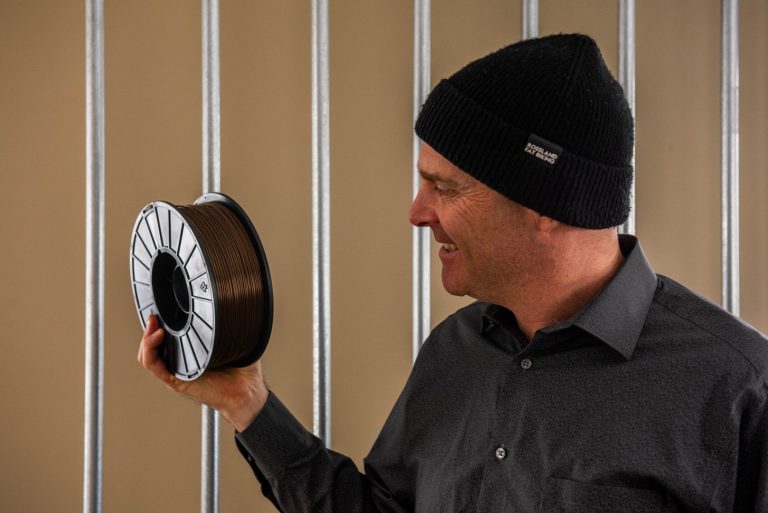
Could you expand on how your materials are carbon negative?
Of course; as we produce our materials, the trees are sequestering carbon. And then during production it’s a very minimal emission process because of our closed-loop system, which doesn’t generate any waste. So if you register the total carbon emissions from the process, the amount of carbon that it captures is much more. than what it produces. We’re not harming the planet during production; we’re actually reducing the carbon that’s in the atmosphere – which is, of course, one of the goals from the Paris Accord. And then at the end of product life, our products degrade into compounds that are helpful to the soil and to the planet. There are many possible solutions to the complex challenges the world is facing, but finding a solution for what happens to products at the end of life is important. Usually, there’s a handful of things that might happen: either it gets littered, it gets landfilled, it gets burned, or it gets recycled. So in any one of those scenarios, our materials are helpful; they’re either carbon negative or carbon neutral. Even if it’s littered, it acts more like a piece of wood in the ocean than a piece of typical plastic. Of course, littering is a societal issue that we also need to try to change, but changing the way everyone acts is another challenge.
It sure is. Could you elaborate on how you grow sustainable resources and turn them into plastic?
The precise source of any bioplastic is quite critical. Growing crops on farmland, for example, comes with difficulties; you’re using precious space that should maybe be used to grow food rather than materials for products, even if they’re bioplastics. We don’t use valuable agricultural land, because that’s not in harmony with what the planet needs. Even using fertilizers causes issues; the emissions are detrimental, and chemical fertilizers cause nutrient runoffs. We don’t want to move things in the wrong direction and add more carbon to our atmosphere. That’s why we use waste wood. It comes from trees that are grown on the side of the mountains, so they aren’t fertilized. Or, if they are fertilized – as in some cases – we’ll use wood sourced from trees that solve environmental challenges, like remediating the pollution that a landfill creates. We work with companies that use these trees in potentially polluted areas; they collect pollutants from sites like landfills – it’s called leachate – and as it’s washed with rainwater it comes out in an ugly liquid, which they water the trees with. The trees remediate the liquid, filtering it like a sponge. We then separate the wood from those trees into its three main components – resins, fibres, and sugars – to make our biomaterials. Our particular specialty is the glues from the resins. We are unique in how we handle those, and although it sounds similar, it’s different from what a pulp mill does. Our process separates the wood into its highest value components in a much more thoughtful way. I’m not criticizing pulp mills, but the way pulping works hasn’t really been majorly innovated for many years.
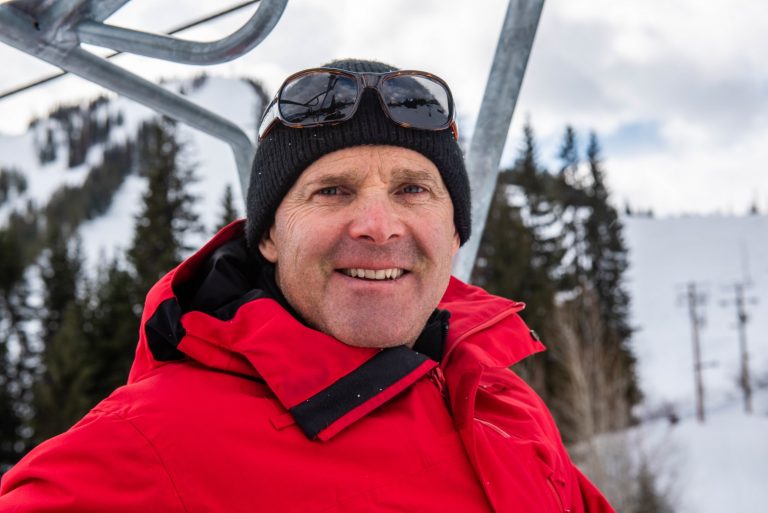
What’s your overall goal?
Our current goal is to get a secure foothold in the marketplace. As I’m sure you can imagine, it’s such a large forum that the competing prices are a challenge, especially when you’re dealing with existing systems and an industry that is 200 years old and at full scale. But we’re making sustainable products that perform – they’re lighter, stronger, and more heat resistant than the incumbents’ products – at a competitive price. We’re also future-proofing jobs. We’re aiming to reach a scalable size and secure market share by targeting high-value niche markets. How this has been working so far is we develop the products and then develop the markets for it; we show that there’s the demand, then we get the financing to build the plant to supply that demand. Because it’s a new process, it’s necessary to basically prototype and then demonstrate what can be done with our materials. For example, the 3D filaments we’ve produced are now in demand with the 3D printing community. Our biodegradable plastics are also highly in demand right now; companies that want to have a sustainable product have really been our niche. Businesses understand that if they can make their products more sustainable, then they have a better sustainability report and their share price goes up. Plus, consumers like you and me are increasingly prioritizing purchasing sustainable materials, so every company out there is trying to revamp their production plan. You could list almost any Fortune 500 company, and they’re talking to us. So we’re currently proving sales to justify the investment it takes for us to scale.
How have you successfully set up your business in Metal Tech Alley?
We’re located at MIDAS in Trail, where we have five employees, but we contract a lot of work out. We’re part of the Biocomposite network, so we have over 32 researchers working with us in that resource base alone. It’s a government initiative that’s really helped us. We also work with a number of other organizations, like the National Research Council of Canada (NRC), and universities in the US, like the University of Idaho. We’ve had tremendous support locally from Community Futures and the Columbia Basin Trust, and huge support from the BC and federal governments, too. There’s a huge support network for sustainable materials; I think everyone grasps the vision and wants to see this industry be successful. There’s a long-standing tradition of entrepreneurs in this region, people who are out-of-the-box thinkers, and people who are willing to take on challenges. I think that entrepreneurial spirit is inherent in our community. It’s exciting, and it’s a natural fit for us to be in Metal Tech Alley.
Why is this mission so important to you?
I really want to raise the standard of living for the planet. I think that people have become overwhelmed and may be giving up hope that we can achieve both – that we can act in harmony with the planet and have a great standard of living and employment. I really want people to understand that we can make these products superior in performance and cost as well as in sustainability. I truly believe that’s what’s coming, and it’s not really that ingenuitive; all we’re doing is utilizing what the planet has given us in a harmonious way. It’s just the next logical step. I think the real truth is that the planet is getting healthier as we strive every day to make improvements. We’re getting better, and we’ll continue to get better. I believe we can act in a simpler, more conscientious way and simultaneously have a technologically advanced planet that properly utilizes what’s been given to us. I keep going back to the word harmony because I think words like sustainable are greenwashed a lot – biodegradable is incredibly greenwashed.
Greenwashing is convincing the consumer that a product is sustainable through marketing and lack of transparency. For example, some companies mix plant-based plastic with regular oil-based plastic for products like water bottles. The truth is that this causes even more carbon emissions and is worse for the environment in comparison with the original plastic bottle, but it’s worth it for them to be able to advertise plant-based plastic products.
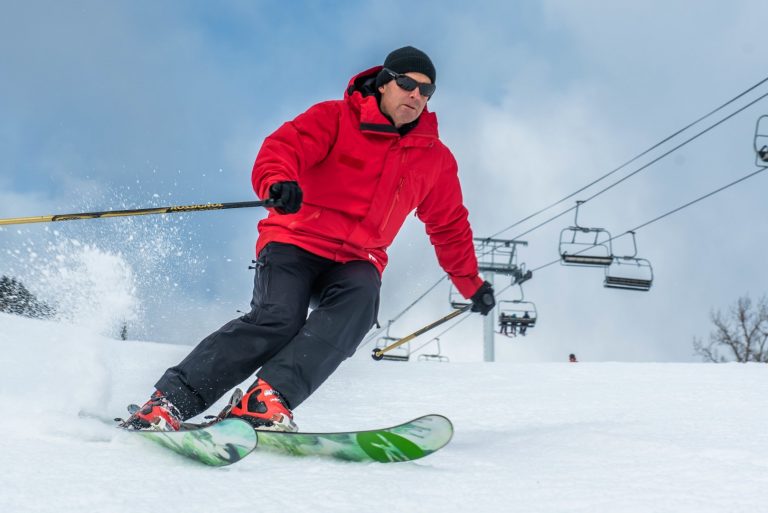
And lastly, other than the environment, what’s special to you about the region?
For me, living here isn’t just a lifestyle, it’s in my soul. My kids are the sixth generation of my family living in the area. My great-great-great-grandparents were some of the original entrepreneurs responsible for helping define and open up this region. My grandparents were some of the engineers for the local mines, and my family all lived in Rossland while it was developing. Today my family all lives locally. We’ve always been committed to sustainable long-term economic growth for the area, in terms of jobs and improving the lifestyle here. It feels good to be surrounded by the souls of my relatives and friends. And we’re all here making our own reality, so why not make it really really great?